Process Cost Analysis Assignment Help
What do you mean by process costing?
Process costing is basically methodology which is used in the accounting field which traces the direct costs from its rots ad also accumulates the direct costs. Process accounting helps in allocating the indirect costs which are directly related to the manufacturing process. As we know, costs are mostly tagged with the products or services which are produced or distributed as a large batch. This also includes having one whole month’s production and distribution chart. These costs are then allocated to the respected individual units of the good. Process costing then assigns the basic average cost of the production on each of the units, which is an opposite extreme of the job costing procedures which elaborates the process of measuring of individual costs of production of each individual unit. Process costing, in simpler words is a method of managing and assigning the costs to the respective units of the goods produced by any firm, which mainly includes production of large quantities of goods of homogenous products. Process costing can also be termed as an operation type which is primarily used for the casting out of the product cost at each and every stage of production or manufacturing. The market industries and business firms who produce homogenous products and whose production process is in a complete state of continuous processing, then process costing is the best suitable way for them. A major process can be related primarily to as the sub-unit of an elaborated organization, which is specifically defined for the cost collection purpose.
Our tutors are professionals from universities and high schools which have excelled in their projective field. When students are distraught in this subject study and are not getting any good understanding from it, we come then. Our tutors are highly professionals in this field. Apart from helping in the projects an assignments completion, they also provide relevant notes on the topic for the students.
What is the importance of process costing?
Process costing is a very important aspect of the cost accounting of any firm. It manages and authorizes many other field of operation in an organization with its working. Costing is related to all the pricing as well as the manufacturing costs related things about the product that the particular company produces. The companies engage their resources and manpower for keeping the track of their cash flows, about where their money is being spent in the distribution as well as the production stages. The first step of this is to understanding of these costs for being able to control them as per needs. It is a very important part and needs expert supervision when the company chooses the most appropriate type of the costing system as per their product and industries stature. This enables them to make commandments with the costing and help it make the better of the company’s profit. There is process costing and job costing. Some companies or business firms uses both types of costing, some use job costing only and some use process costing only. Process costing helps immensely in predicting the average costs per product which is being produced and manufactured. The process costing technique is also very convenient as it requires less book keeping than the usual job order costing technique. Hence, due to this most of the companies opt for the process costing technique as it saves their time as well as manpower, and eventually they can look after other fields too.
When is the process costing applied?

Process Cost Analysis Assignment Help By Online Tutoring and Guided Sessions from AssignmentHelp.Net
Process costing is usually applied when the company is producing large quantities of homogenous products and at a continuous speed. The company or business firm produces a healthy units of goods through a set operation or a prolonged process over a period of time, like a month or four weeks. It is also applied when one particular order is not affecting the overall production process and maintains a standardization of the process and the product exists. However, as we know, there is a significant change in the costs of various other products, the process costing technique would not be able to fully provide with the adequate product cost information and its specifications. Costing is primarily used in the mainstream industries of chemicals, paper, plastic, glass, coal mining, petroleum, textiles, courier, food, cement, banks, soap, appliances, etc.
What are the main reasons for the usage of Process costing?
The main reason for which this technique issued are:
- The quantity of production and distribution of the goods and services is very high during a specific period of time.
- The products are manufactured in large quantities but is sold in smaller quantities and usually one product at a time, for example, automobiles and bread.
- When the managers managing the cost fields need to maintain the cost control over the processes of manufacturing as well as the distribution. This technique of costing provides the managers with equivalent feedback over a period of time. The feedback can used over a period of time for comparing the results of the firm’s variations in costing and pricing parts. By this, the costs system is kept intact with the projected manufacturing budgets.
- The production costs is diverted from the finished goods to the final costs of goods sold as much as the new sales are made. This primarily requires the accurate and correct accounting steps and procedures and accounting of products cost per single unit. It is required for a basic matching of a production and good costs as opposed to the related sales revenue.
- Materials part way through a process, for example. Chemicals and particles which might need to be given a specific value and moreover process costing allows extensively for this. When it is determined what the particular cost of the part which is processed material has incurred, such as an equivalent unit or labor directly relative to the processed value of a finished process can be accurately calculated.
There are basically two types of analysis in the cost accounting, one is process cost analysis and the other one is cost analysis. Name are somewhat similar of both and the classifications also but there are some differences. Sometimes students gets heavily confused in this thing. Differentiating between cot analysis and process cost analysis, doing this will take up time and hence students are not able to complete their projects and assignments. But don’t worry we are here, to get on with you projects and work with you. We assign tutors for this job. Our tutors ensure a 100% plagiarism free work and also completion of the projects within the deadline. Apart from process cost analysis Assignment Help, we also provide homework completion and projects completion. Visit our website assignmenthelp.net or simple contact us on our helpline number, to know more about the services.
Understanding process industry
Some industries like oil refineries, sugar mills, milk products industry, run several sequential processes to get the final output. Input is put in the first process; output of the first process is transferred as input of the second process. This continues until the final product comes out of the end process. See the process diagram given in figure 7.1. Input is put in process-I. It comes out as final product in process-III. Process-II receives the output of process-I and process-III receives the output of process-II. Of course, it is possible to sell the output of process-I or process-II, if the market for such intermediate products exists.
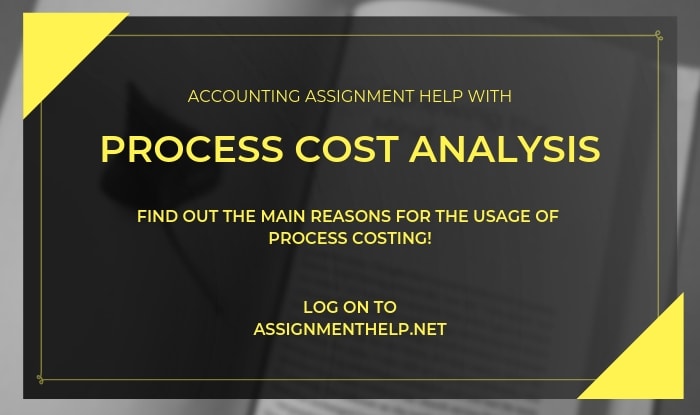