Methodology Finalized Project Sample Assignment
Following chart shows methodology for achieving the aim
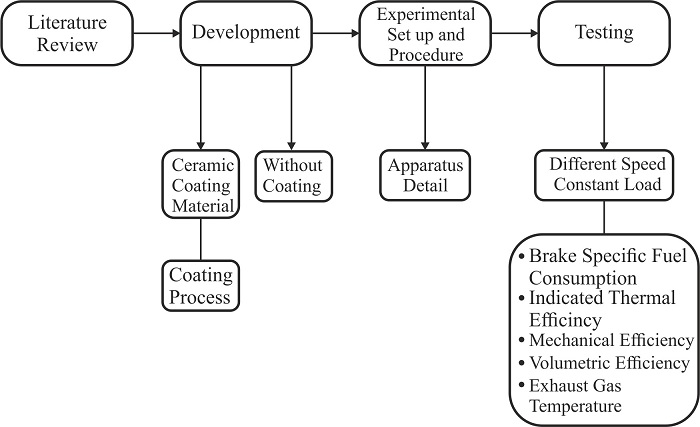
Flow Chart 1. Methodology of Experiment
Chart explain that how to achieve the aim (target) to follows the methodology. In this Literature review, The development of project is essentially determined by the possibility of creating and of producing, in sufficient quantities, structural materials meeting the requirements of modern technology. A trend to use high and low temperatures, low and high pressures, high rates of gas flow and concentrated energy fluxes in all modern fields of engine working industries—power and transport.
1 INTRODUCTION
In modern age, there is decreasing the natural sources of fossil fuels which are the best source of fuel of vehicles for running. The alternatives to current fossil based fuels for propulsion and power generation fuel properties are important criteria from a combustion point of view to take into consideration, since the combustion behavior relates to the main purpose of the heat machine, i.e., to convert chemical power to mechanical power. However, the fuel in an internal combustion engine undergoes other processes and passes many systems before it is burned. New inventions and researches are proved very beneficial for overcoming this problem economically and increased the efficiency of engine. Natural gas is a fossil fuel found in nature reserves, associated or not with petroleum. The cost of obtaining from nature is lower than other fossil fuels. Natural gas consists of about 90% methane, 3% ethane, 3% nitrogen, 2% propane and other trace gases. Methane which is the always dominant component of natural gas is the first member of alkane’s family. Since it has a high H/C ratio, natural gas is known as the cleanest fuel in fossil fuels. Due to its ecological benefits, city buses operate with natural gas engines in many countries. CO2 gas, which should normally be between 180 and 280 ppm in the atmosphere, reached 405 ppm as of September 2018 due to overuse of fossil fuels.Engine has been under the observation of many researchers [12]. The commercial fuels a number of additives are added to ensure special characteristics of the fuel, apart from the main energy carrying components. These include biofuels as ethanol and other oxygenates such as MTBE (Methyl Tert-Butyl Ether) for gasoline and FAME, HVO (Hydrotrated Vegetable Oil) for diesel. Engine performance increased by working on various engine materials and researchers have used metallic coating in high temperature and pressure conditions which is sustainable for the system. For various operating conditions, engine performance and efficiency improve by using good advance material and cooling system. In automobile industry, ceramic coating announces revolution. Theoretical results on improvement of the engine performance are good but experimental results are different. It is observed that air-fuel ratio and peak condition of diesel engine remains constant [14]. Coating of Yttria Stabilized Zirconia (YSZ) on piston head gives insulation and acquire adiabatic condition. No heat enters or evolve the system in adiabatic process that increases the heat in combustion chamber. Then thermal efficiency of the engine goes up. Air density decreases due to increases in temperature in combustion chamber which results in decrease of volumetric efficiency.
Experiment was done on two different thickness of ceramic coating material and without coating base piston. Coating thickness is 0.5mm and 1.0mm. Results show that there is decrease of 6% in brake thermal efficiency but speed increased in 1.0mm coated piston head. Brake thermal efficiency in 0.5mm coated piston head increased up to 10%. The comparison was take with conventional engine. The temperature of exhaust gases in 1.0mm coated piston head increased by 10°C comparing with 0.5mm coated engine and baseline engine. Volumetric efficiency goes down while increasing the thickness of coating Dennis Assanis et al [1].
Heat losses reduced by the thermal barrier coated engine from which indicated thermal efficiency of the engine increased. In an experiment, piston head was coated with Titanium dioxide on diesel engine piston. Atmospheric plasma spray method was used for coating. Engine was set at 1500 rpm for coated and non coated piston. The performance of the engine was checked at different load of 2,4,6 and 10 kg in constant 1500 rpm. In coated piston engine, brake specific fuel consumption decreases more than base non coated piston engine. Brake thermal efficiency increased up to 3% by coated engine by comparing with conventional one. Non coated engine increased indicated thermal efficiency by 3%. Mechanical efficiency for coated piston engine increased up to 2% Suresh Kumar Rupangudi et al [2].
Experiment conducted for both coated and non coated engine with different load, speed and injection timing. It is finalized that in improving thermal efficiency, brake power and indicated power piston crown coating is more effective that cylinder head coating. There is decrease in volumetric efficiency. Temperature of exhaust gases of thinly coated piston crown engine has higher than cylinder head coated engine when compared with conventional engine. Peak cylinder pressure of base engine has higher than the cylinder head coated engine and piston crown coated engine. Specific fuel consumption of baseline engine was higher than piston head coated engine E. M. Afify,D. E. Kleft [3].
Effect of thermal barrier coating is observed on performance, combustion and emission. Insulated piston compared with conventional one. Insulated piston engine has high thermal, mechanical efficiencies and brake power than base engine. SiC and ZrO2-Al2O3 are the materials which are coated on pistons and checked with conventional engine. ZrO2-Al2O3 coated engine has more brake thermal efficiency comparing with SiC and non coated engine [4].
Effect of thin ceramic coating has studied in spark ignition engine. A modified 2.5-liter GM engine with ceramic coated piston, liner, head and valves were used Dennis N. Assanis and Tarun Mathur [5]. Experimental results of coated piston engine compared with convention petrol engine. Ceramic coating helps in achieving the 18% higher brake power and 10% lower in specific fuel consumption.
Experiment conducted on engine performance and exhaust gases of an adiabatic engine by coating ceramic material YCZ in combustion chamber and compared with conventional one. Results tell that thermal efficiency increased, brake specific fuel consumption decreased. Experiment was studied in various conditions like fuel flow, exhaust temperature, exhaust emission. There is improvement in performance and emission in results [6].
Insulation in the engine is given to reduce heat losses and increase the thermal efficiency and less emissions to environment. Brake specific fuel consumption for coated engine decreased more than the non coated engine with increasing brake power. Brake thermal efficiency increases up to 3% comparing with non coated one. Mechanical efficiency increased 2% more than baseline engine. For coated engine air-fuel ratio is higher than non coated. There is little increase in exhaust gas temperature in coated engine than non coated engine Suresh Kumar Rupangudi et al [7].
Thermal barrier coating gives insulation which decrease heat losses. Thermal barrier coating engine performance and emission results compared with base engine. Benefits of thermal barrier coatings in IC engines are higher engine efficiency; Lower pollutant emission; Lower fuel consumption; Low cetane fuels may be used; Smaller ignition delay; Lowe size and weight of the engine. Brake specific fuel consumption of coated engine is decreased kg/KWh, Brake thermal efficiency of coated engine is increased by 5.99% when compared with conventional engine. Hydrocarbon emissions was decreased as compare to baseline engine Jayaram MUTHUSAMY et al [8].
[9] The thermal barrier coating of Al2O3-TiO2 and ZrO2-Y2O3 with NiCrAl bond coat effected the temperature and stress distribution on the piston crown. Temperature and stresses distribution decrease with increasing distance from free surface. Temperature on the coated piston increases and performance of engine goes up so the power of engine increases approx. 8%. [10] Analyze the thermal barrier coating on the piston surface of diesel engine performance. The ZrO2-Y2O3 coating enhances the performance, fatigue lifetime and pollution contents of the engine. The reduction of temperature gradient and thermos-mechanical stress from which fatigue life of piston increases.
[11] The huge amount of energy transfer to environment in the form of thermal waste in internal combustion engine. Combustion of air-fuel is inside the engine cylinder. Working pressure and temperature inside the engine cylinder is very much high; hence special alloys are used. In combustion engine high grade fuels are used with proper filtration Higher efficiency about 35-40% Lesser requirement of water. Thin coating of ceramic material to the aluminum based alloy piston reduced the thermal waste which is used as useful work. Thermal barrier coating of ceramics reduces the mass of fuel consumption by 4.12%. thermal efficiency goes up by 12%, specific fuel consumption goes down by 2.65% and exhaust gases reduced.
In this experiment, working done on 4-stroke single cylinder petrol engine with over head valve and cylinder is inclined at 25° angle and there is horizontal shaft for power transfer and coating purpose is to protect from the conduction of heat at the same time it increases the thermal efficiency of the engine and comparing with non coated engine coating condenses harmful gases from the emissions. At various loads, diesel engine with ceramic coated piston performed practically. Coating material is Yttria Stabilized Zirconia (YSZ). Coating behaves as an insulation which increases the heat at combustion chamber. Brake thermal efficiency of the ceramic coated piston engine increases because it relies on fuel consumption and fuel consumption is low in ceramic coated piston engine, this factor causes the increase in thermal efficiency. Volumetric efficiency of the engine decreases. Brake power depends upon brake thermal efficiency so being decrease in brake thermal efficiency, brake power of the engine increases because there is inverse relation between them. There in one more factor which is under consideration that is temperature of emissions and it increases because of the complete fuel consumption in combustion chamber. All data compared with the results of standard engine. In all loads, brake thermal efficiency of coated piston engine increased. Because of complete combustion and high pressure, engine releases heat more rapidly which can reduce the thermal fatigue of the piston.
3.2 Internal Combustion Engine Efficiency
The 'thermal efficiency' is sometimes called the energy efficiency. For engines where a fuel is burned there are two types of thermal efficiency: indicated thermal efficiency and brake thermal efficiency. This efficiency is only appropriate when comparing similar types or similar devices. For other systems the specifics of the calculations of efficiency vary but the non-dimensional input is still the same. Efficiency = Output energy / input energy
The second law of thermodynamics puts a fundamental limit on the thermal efficiency of all heat engines. Even an ideal, frictionless engine can't convert anywhere near 100% of its input heat into work. The limiting factors are the temperature at which the heat enters the engine, TH and the temperature of the environment into which the engine exhausts its waste heat, TC measured in an absolute scale, such as the Kelvin or Rankine scale. From Carnot's theorem, for any engine working between these two temperatures. Real engines have many departures from ideal behavior that waste energy, reducing actual efficiencies far below the theoretical values. For energy-conversion heating devices their peak steady-state thermal efficiency is often stated, e.g., 'this furnace is 90% efficient', but a more detailed measure of seasonal energy effectiveness.
3.2 Ceramic Coating Material
Good adhesion is produced by reaction and fusion of the Special’s Ceramic Coating with the base metal. Since moisture or rust cannot penetrate beneath the Special’s Ceramic coating, it will not flake away from exposed edges or damaged areas. The coating does not tend to "creep" under service conditions as can be shown by salt spray testing. CERAMIC COATED metal will flex with the metal providing resistance to stresses that cannot be obtained in solid glass. Ceramic Coating increases base metal flexural strength. Thus, the stiffening effect of the coating can be used advantageously to reduce metal thickness in certain applications. The stiffening effect is more pronounced on lighter gages than on heavier gages of metal. Though thicker Special’s Ceramic Coatings may be used to promote needed rigidity or offer added wear protection, thinner coatings are much less vulnerable to fracture and chipping. Special Ceramic Coating is not a thermal insulator, but it is a relatively good heat conductor when applied in thin coats. Its emissivity characteristics are particularly good. Normally, Special Ceramic Coatings are applied so thin there is only a very small temperature gradient through them. Thermal conductivity is expressed as 0.001 - 0.003 cal./sq. cm./sec/degree C.
Zirconia is the ceramic material which is used for thermal barrier coating and its properties are given below in table
Table 1 Properties of the Ceramic coating Material
Poisson’s Ratio |
0.27 |
Molar Mass |
79.87 g/mol |
Melting Point |
1870 °C |
Boiling Point |
2972 °C |
Thermal Conductivity (25 °C) |
11,7 W/mK |
Modulus of Elasticity |
230 GPa |
Micro Hardness (HV0.5) |
880 |
Density |
4 g/cm3 |
Fracture Toughness |
3.2 Mpa.m-1/2 |
Compressive Strength |
680MPa |
Zirconia (ZrO2) can be found in cubical, tetragonal and monolithic forms. All have different structure from each other. Monolithic has stable temperature 1170°C and tetragonal has 2379°C while for the cubic it is above the 2379°C. Zirconia stabilized with yttria (Y2O3) which gives the finest properties. Zirconia, being ceramic material stay stabilized by calcium oxide and magnesia. Naturally zirconia occurred in monoclinic crystalline structure. The most beneficial ceramic material is zirconia dioxide which has monoclinic structure at room temperature and converts its structure to tetragonal and cubic when temperature of material reaches to high value. Change in volume occurs while moving from monoclinic to cubical structure and this change produces high stresses in material from this crack produces in material upon cooling from high temperature. When zirconia reacts with other oxides it then the tetragonal or cubic structure stay stabilized. Zirconia is always useful in a stabilized state. On heating zirconia converts into a new form if we add some yttria then this change reverses. 2410°C is the melting point of yttria and it remains stable when exposes with air. Melting point cannot achieve easily. Special Ceramic coatings resist the corrosive effects of acid and alkali solutions at the elevated temperatures required for many industrial processes and reactions. These coatings provide both protection of the metal and ease of cleaning. The smooth, abrasion resistant surfaces also allow for more efficient flow of fluids over the surfaces.
3.3 Coating Process
Technique used for coating is plasma spray method. Information about the coating process is given in below table 2.
Table 2 Specification of Coating Process
Coating Process |
Plasma spray Process |
Material |
Zirconia (ZrO3) |
Material coating |
0.2 mm |
Binder |
NiCrAl |
Binder coating |
0.1 mm |
Plasma spray uses combustible gas as a heat source to melt the coating material. Plasma spray guns are available to spray materials in either rod, wire, or powder form. Most flame spray guns can be adapted to use several combinations of gases to balance operating cost and coating properties. Acetylene, propane, methyl-acetylene-propadiene (MAPP) gas, and hydrogen, along with oxygen, are commonly used flame spray gases. In plasma spraying the coating is formed by molten particles being brought onto the substrate by the plasma jet. Both plasma spraying of rods and wires and complete melting of the sputtered material is achieved when wires or rods are melted by plasma jet.
Plasma spray coating is method in which heated materials are sprayed into the surface. There are two primary preferences primarily. First, it can be done at higher temperature in which melting of other known materials can be occur and second it can provide better heat transfer by others. In this method, materials which are in powder form and have some specific size can use easily. The main purpose of using plasma spray coating is to make a thin layer that has high protection values over a non-costly surface. Material places in the form of powder in this method then enters in plasma jet and it comes from plasma torch. Temperature in jet is 10,000 K which melts the material and run towards the substrate and at this place melted material deposited rapidly. There are two variants: Spray and fuse, and spray fuse. In spray and fuse, the fusion is done after deposition using one of several techniques, such as flame or torch, induction, or vacuum, inert, or hydrogen furnaces. In spray-fuse, the deposition and fusion are done simultaneously.
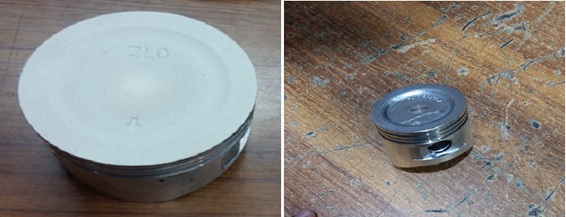
Figure 1. Coated and Non Coated Piston Head
3.4 Experimental setup and procedure
Single cylinder 4-stroke spark ignition engine is used in this experiment. Four stroke cycle engine s is working at completed four stroke of the piston or two revoluation of the crank shaft it is called as four stroke engine. It has 68mm bore and 45mm stroke length. Power of the engine at study time is 3.5kW (4.8HP) and there is 3600 rpm. Engine showed in below figure 2. Electrical dynamometer (is an apparatus for measuring the mechanical power generated, or absorbed by a rotating machine) linked with petrol engine for study the power output. There are several parameters which are to be measured by this engine set up like fuel consumption, load, engine speed, cooling water temperature, inlet exhaust and air gas temperature etc.
Table 3 Engine Specifications
Engine Type |
Four-stroke single cylinder OVH petrol engine |
Dry Weight |
15.1 kg |
Engine Oil Capacity |
0.6 Liter |
Starter |
Recoil |
Net Power |
3.6 kW (4.8 HP) / 3600 rpm |
Displacement |
163 cm^3 |
Cylinder Sleeve Type |
Cast iron sleeve |
Bore x Stroke |
68 x 45 mm |
Ignition System |
Transistorized |
Fuel Tank Capacity |
3.1 Liter |
Dimension (L x W x H) |
312 x 362 x 346 mm |
Max. net torque |
10.3 Nm (1.05 kgfm) / 2500 rpm |
Cont. rated Power |
2.5 kW (3.4 HP) / 3000 rpm 2.9 kW (3.9 HP) / 3600 rpm |
Compression Ratio |
9.0:1 |
Fuel cons. At cont. rated power |
1.4 L/h - 3600 rpm |
IC engine explain that Intake valves of most IC engines are poppet valves that are spring loaded closed and pushed open at the proper cycle time by the engine camshaft, shown schematically. Much rarer are rotary valves or sleeve valves, found on some engines. Most valves and valve seats against which they close are made of hard alloy steel or, in some rarer cases, ceramic. They are connected by hydromechanical or mechanical linkage to the camshaft. Ideally, they would open and close almost instantaneously at the proper times. This is impossible in a mechanical system, and slower openings and closings are necessary to avoid wear, noise, and chatter. The lobes on a camshaft are designed to give quick but smooth opening and closing without bounce at the mechanical interface. This requires some compromise in the speed of valve actuation.
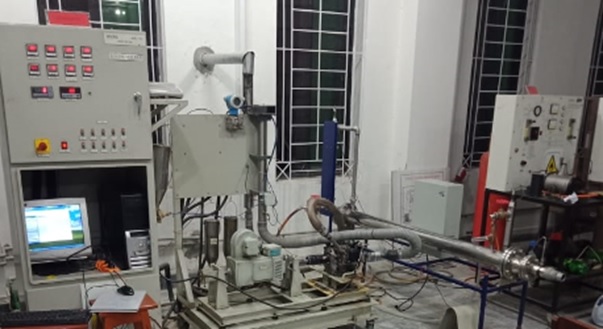
Figure 2. Engine Test Bed(MODEL: THO3)
3.4.2 Procedure
With coated and non coated piston, engine rpm set at 3600. Engine performance calculated with coated and non coated engine at different speed and constant load. The experiments were conducted at four different speeds as 2000, 2500, 3000 and 3500 rpm. Other parameters calculated such as brake specific fuel consumption, brake thermal and indicated thermal efficiencies, mechanical efficiency, brake specific energy consumption, air fuel ratio and exhaust gas temperature obtained. The variations of these parameters except exhaust gas temperature plotted with respect to Engine Speed and variation of exhaust gas temperature plotted with respect to Break Power. Various ways of obtaining variable valve timing are being developed for automobile engines. These allow intake valve opening and closing to change with engine speed, giving better flow efficiency over a range of speeds. Some engines use a hydraulic-mechanical system that allows for an adjustment in the linkage between the camshaft and valves. It does this with engine oil and bleed holes that require longer cycle time (equal real time) to shift linkage dimensions as speed is increased. In water Dynamometer the friction type can be resulted water as friction medium between the shaft and stationary parts, passive: Can’t be used to motor the engine, slow to altering the resistance offered to the shaft rotation (several seconds).
With proper design, the intake valve can be made to open earlier and close later as engine speed is increased. Some engines have camshafts with dual lobes for each valve. As engine speed changes, the follower that rides the cam shifts from one lobe to the other, changing valve timing. This gives better engine efficiency at a cost of mechanical complexity. In addition to this higher temperature causes the fuel burning to be more complete, which also increases the engine efficiency. Higher temperature in the combustion chamber improves the engine efficiency.
Problem facing during running the IC engine sometimes encountered with carburetors is icing, which usually occurs on the throttle plate. Water vapor in the air will freeze when the air is cooled to low temperatures. Cooling occurs for two reasons: There is expansion cooling due to the pressure reduction experienced by the air as it flows through the carburetor, and there is evaporative cooling due to the just-added fuel droplets in the throat of the venturi. Fuel additives and heating the carburetor are two possible solutions to this problem. Another problem of carburetors is the splitting of the air flow around the throttle plate immediately after the fuel has been added. This makes it very difficult to get homogeneous mixing and is a major reason why the air-fuel mixture delivered to the cylinders is often non-uniform. This problem is more serious with later short barrel, short-runner carburetors.
3.5 Conclusions
A major goal of the development of internal combustion (IC) engines continues to be higher performance and efficiencies. A major aspect of achieving higher performance and efficiencies is based on fundamental thermodynamics. Methodology aiming the use of fossil for fuels and homemade oils to run the IC engine to enhance it’s combustion proficiency. Piston is the most important Instruments used in engines which must be always free from corrosion. Rule of Plasma coating is also imp to run the engine. From experiments we concludes that Engine performance calculated with coated and non coated engine at different speed and constant load is obtained in different fashion. Fuel consumption methodology is discussed briefly in this literature.