.
Solidworks how to model a dynamic spring
- Open SolidWorks and start a new project in Part.
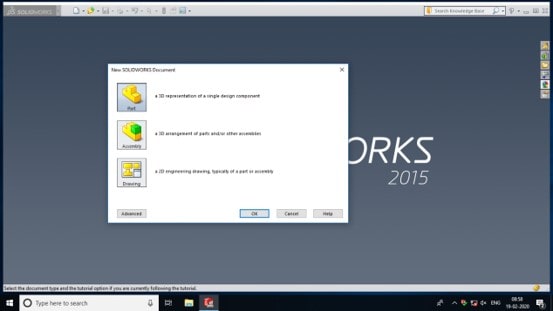
- Use the Sketch option in Front Plane and start editing it. Use the Normal To option to get a flat Front Plane to Draft.
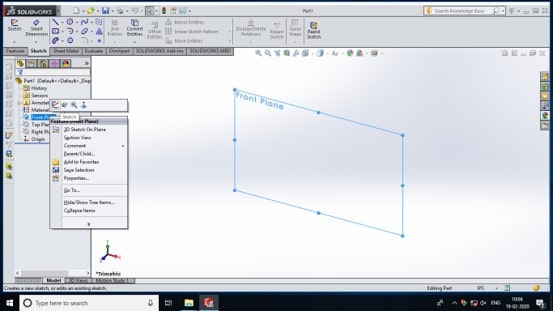
- Select Line and draw a line of any length and close it. Then use the Smart Dimension to alter the dimension as per need. As in this tutorial, I am using a 120 mm line. Make sure that the relation with the origin is Vertical. Then Exit the Sketch.
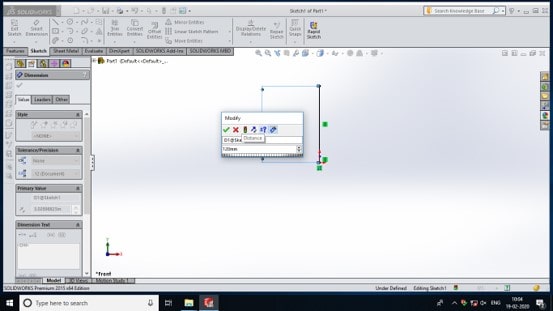
- After that right-click on Front Plane and use the Sketch option to Sketch again. Do not use the same sketch that you used before for the line.
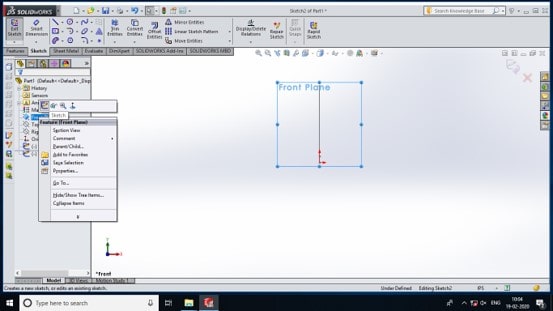
- Draw a circle using circle option somewhere horizontally with the line drawn previously. Do not worry about the dimension we will use Smart Dimension to alter that to 5mm diameter.
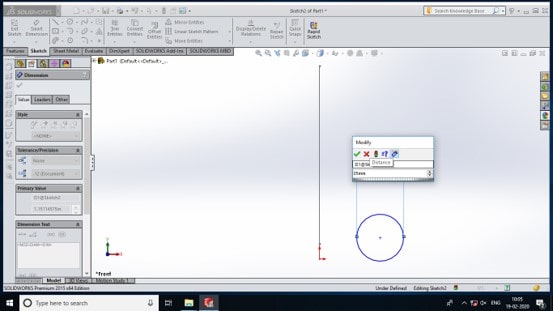
- Now set the relation from the center of the circle to the lower end of the line or origin to horizontal. This can be done by clicking on the center of the circle and pressing the CTRL key and pressing the point of Origin and clicking on Horizontal under add Boundaries.
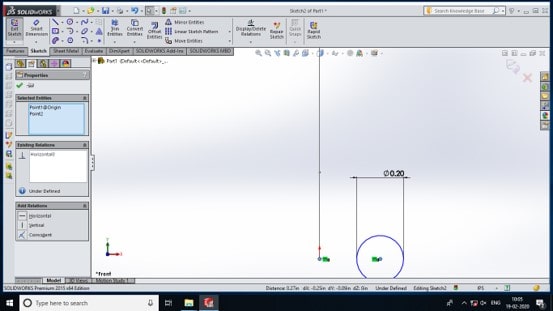
- Once that is done exit the relation dialogue box and select the centerline option from the drop-down menu of lines;
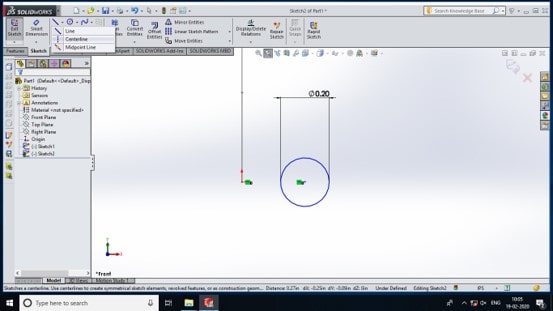
- Use center-line to join the circle and base of the line. Also, use a Smart dimension to alter the distance between them to 25mm.
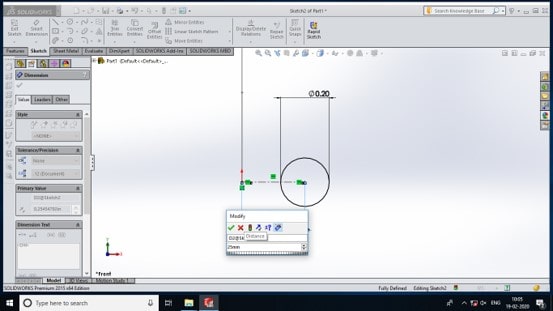
- One all is done you can go ahead and delete all the dimensions once you have exited the Smart Dimension function. Since there is no use for them those dimensions will only make the design bit clumsy.

- Now exit the Sketch option and go to Feature Tab. There Select the Swept Boss/Base option and then select the circle as profile and path as the line under profile and path menu.
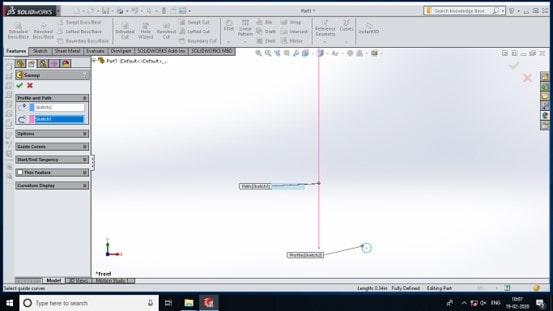
- In the options tab under that in Orientation/twist type select twist along the path with Normal Constant. Change the Define By to Turns and give the number of turns you want in this case I have used 10 turns.
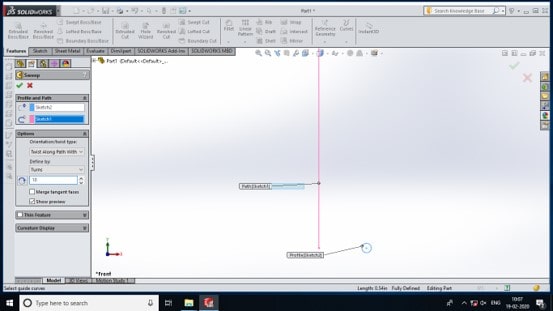
- After that click on the tick, sign to complete the process and you’ll get a model somewhat like the picture given below. After that save the file.
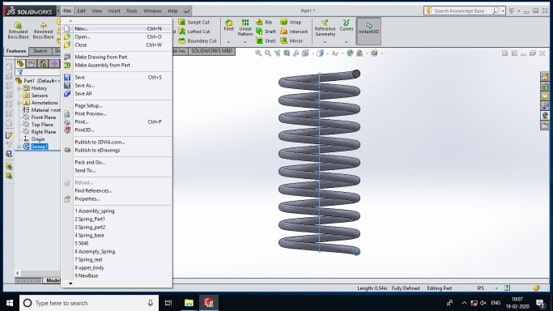
- Open new file under Part option. Select the Top Plane and start drawing a circle from the circle option under the Sketch option. The diameter of the circle may we between 60 to 100 mm. Choose whatever you like to. Use a Smart dimension for the process after drawing circle of any diameter.
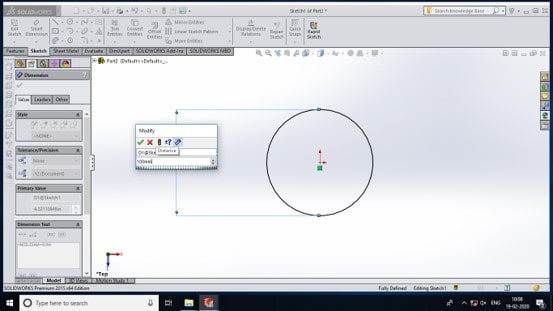
- Now exit the Sketch mode and go the Extruded Boss/Base and select it.
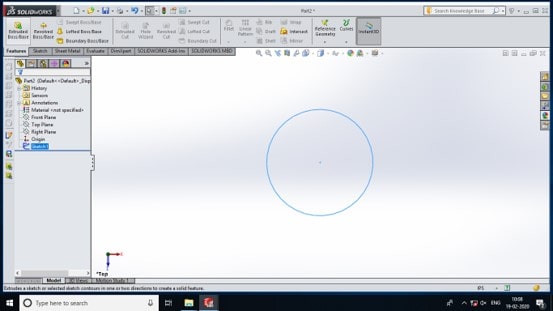
- In Extruded Boss/Base dialog box, give the height or depth to be of 10 mm. Approve the process and move to the next step.
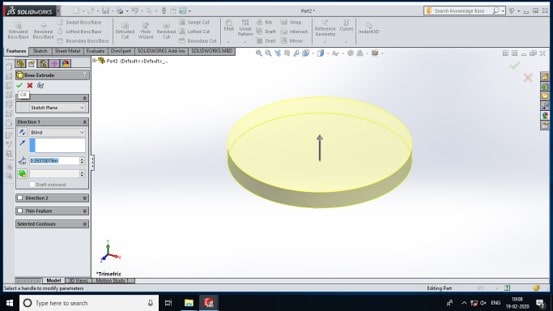
- If you have finished the process correctly you’ll get a model like one given below.
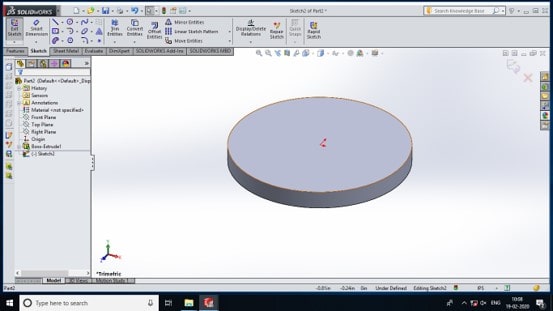
- Now select the top surface of the extruded part and go to Top Plane and draw a circle from the middle of the surface. Don not worry about the dimension.
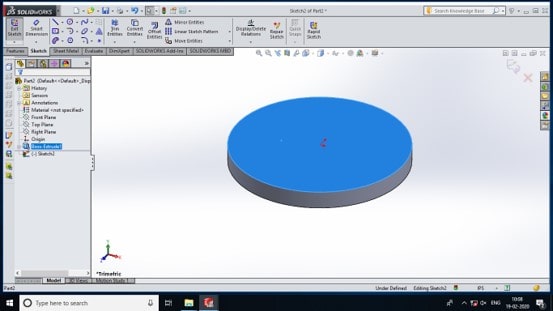
- Use Smart Dimension to give the diameter of small circle to be of 10 mm. Then exit Sketch Mode.
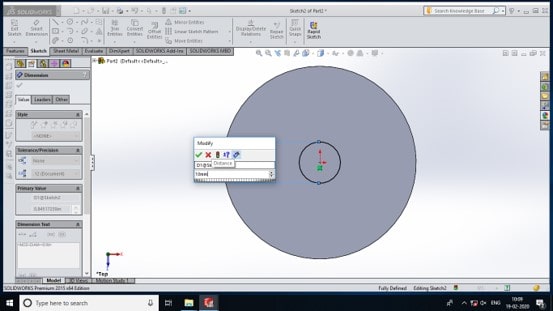
- Now select the Extrude Boss/Base option to create a surface from this circle. The height of the new surface will be of around 200 mm so enter that in the height/depth option.
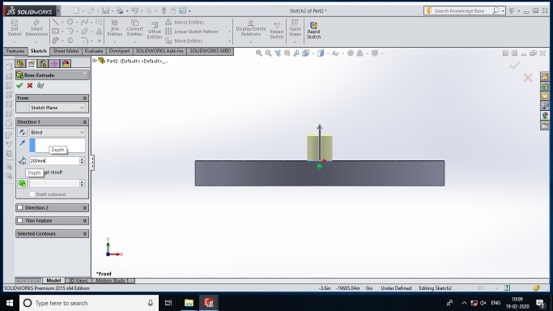
- If you have done everything correctly then the model you’ll get will look like the one given below. Now save this part with any name you want.
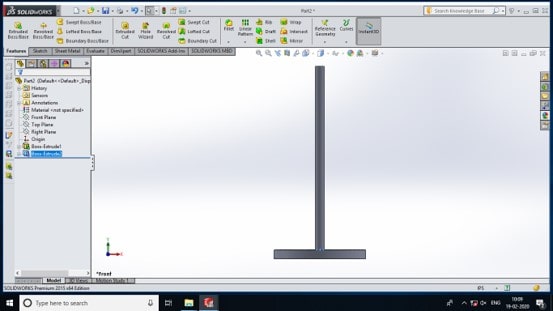
- Open new part and let us now make the last part for the tutorial. Now select the Extruded Boss/Base option. It will redirect you to sketch menu. Select the Top Plane and start working on that.
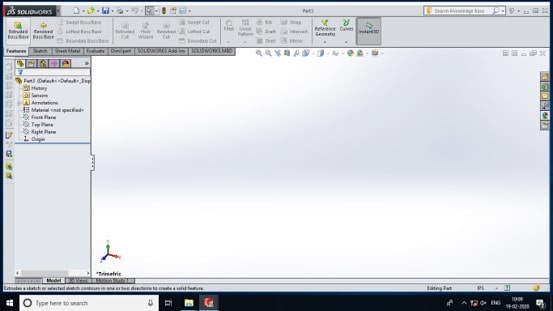
- Now draw a circle of any diameter from the origin of the plane. After finishing the circle approve tit and go to Smart Dimension.
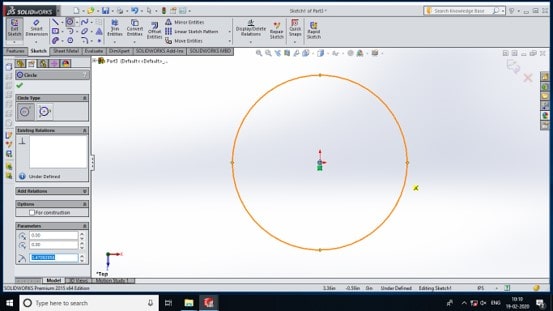
- Select the circle and give the dimension which will be equal to the previous base diameter. I have took 100 mm as the previous one had 100 diameter base.
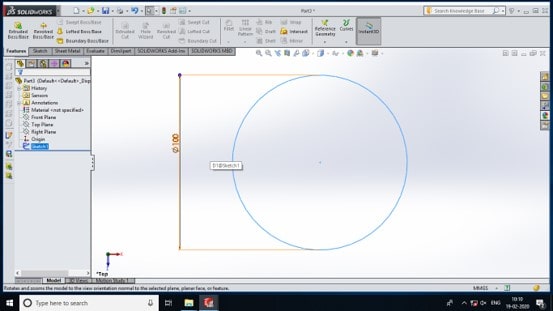
- Now exit the Sketch Method. It will redirect you to Extruded Boss/Base method there give the same height/depth as the previous base. I have given 10 mm for both the surfaces.
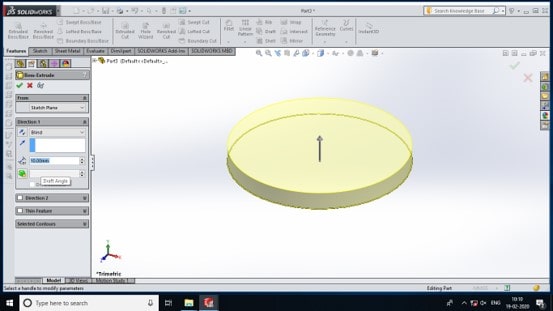
- Select the Extruded Cut Option. This will alert you to select the surface where you want to perform the operation. Select the Top surface. Then it will redirect you to Sketch menu.
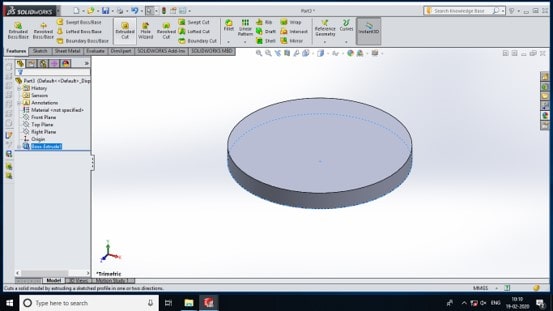
- Now select the Top Plane and then draw a circle from the origin of the Plane and exit it after drawing the circle. Then use the Smart Dimension to give the diameter to be equal to 10 mm and then approve the operation.
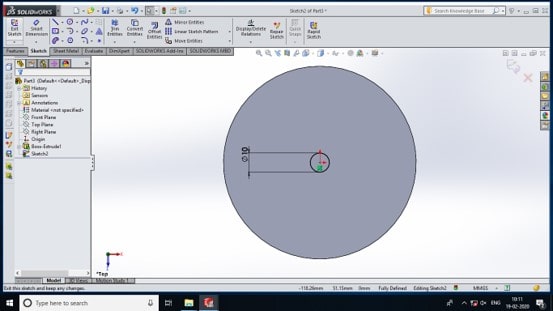
- Select the through all option to cut a hole through the surface from top to bottom. This will ensure there is no mistake in your model.
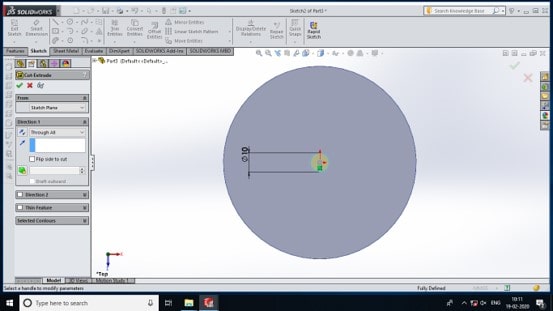
- Approve the process and you’ll get a model like given below if you haven’t made any mistakes during the whole process. Then save this part too.
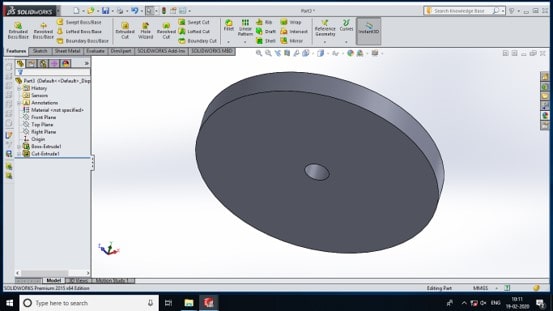
- Now open a new project under Assembly Option.
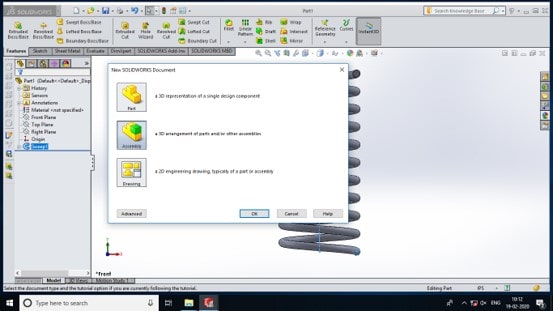
- Now browse to the place where you have saved the parts. If you have drawn nothing except the three parts we drew just before then you’ll see them under the Open documents.
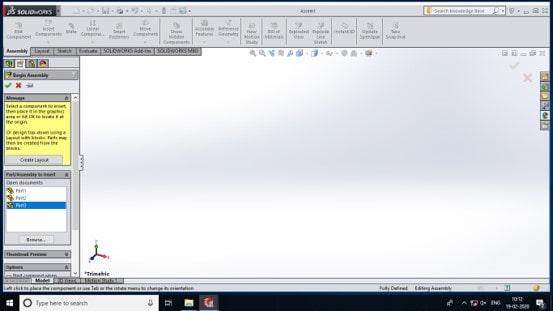
- Drag and drop any part onto the screen.
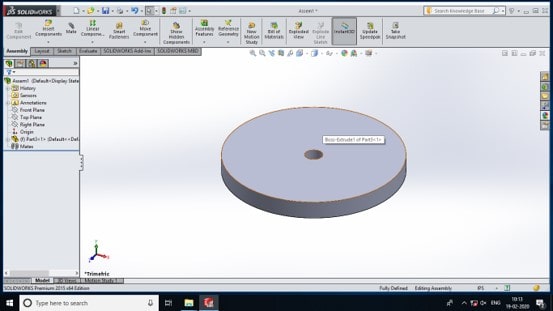
- Then use the Insert Components to insert all the components one by one.
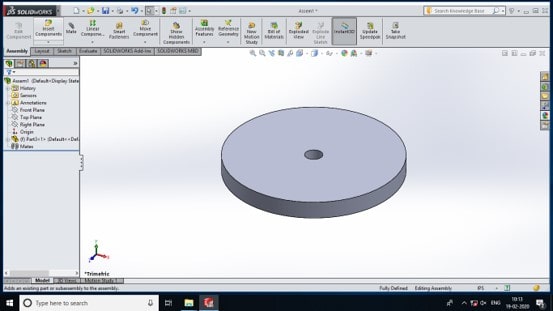
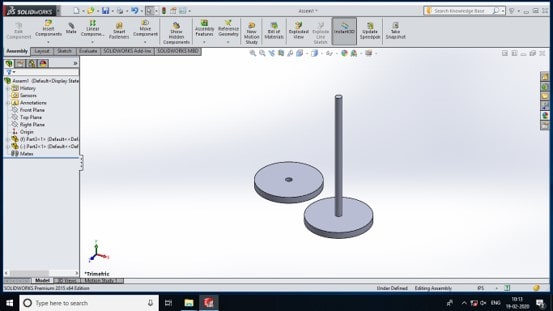
- When all the components are on your screen then let us now mate the different parts so that different constraints can be added between them.
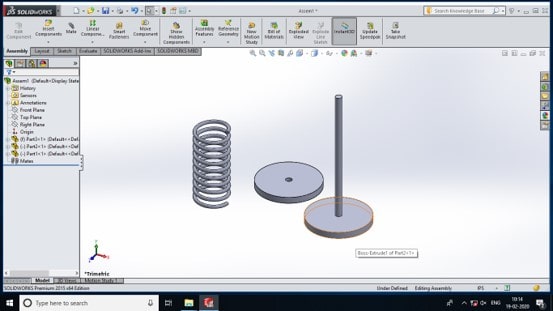
- Now for the two bases, select the bigger curved faces of the both parts and click on mate option.
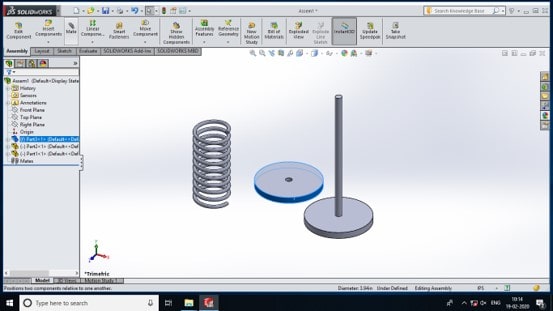
- Use the concentric option so that their centers on the same origin.
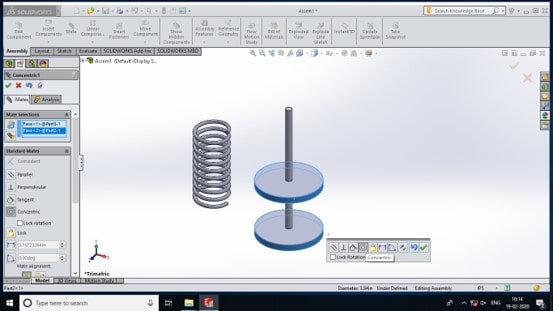
- Select Lock Rotation since we don’t want any rotation between these components.
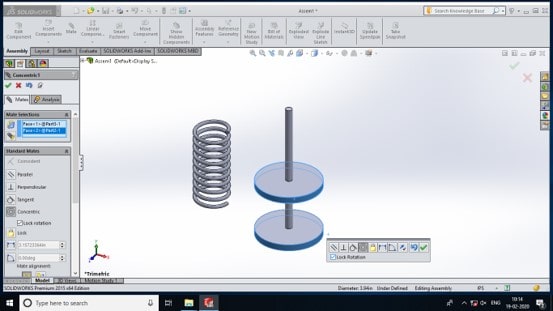
- Now go to the spring sketch and browse to the first sketch in that model. There right-click on the sketch and use the show option so that the of the circle can be seen.
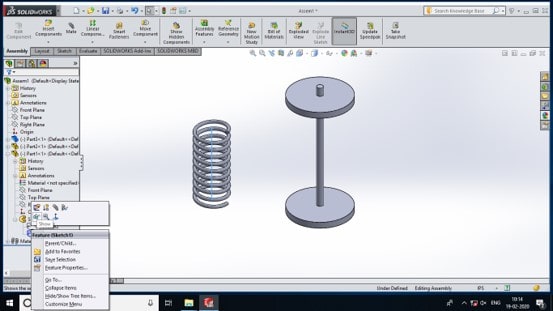
- Now select the lower end of the centerline of the spring to use the mate option. Then select the largest curved surface of the second model or base to mate it with that. Again use concentric option. Then click on tick sign to approve this mate.
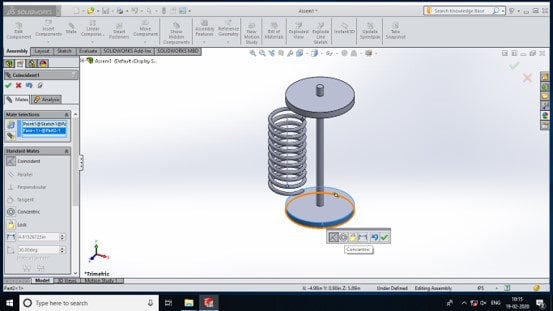
- Now select the upper end of the spring center-line and mate it with the same base curved surface. Approve this too complete this task.
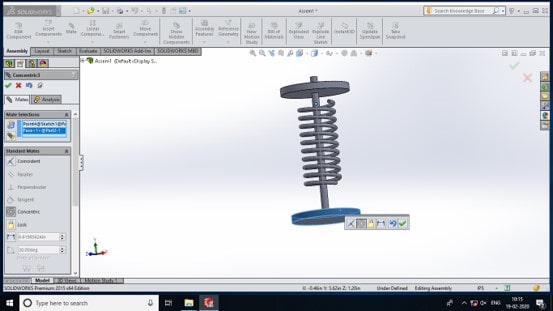
- Now go the browse to the sketch 2 of the spring model under the Sweep 1 and click on exit sketch option when you right-click on the sketch 2.
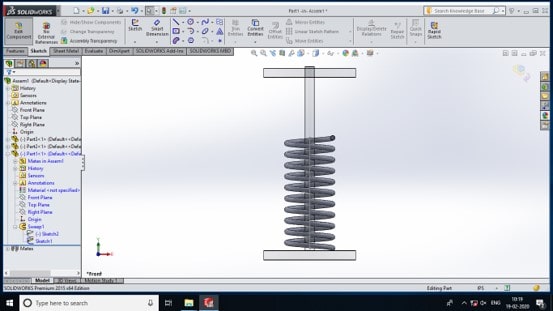
- Now select the smart dimension and get the dimension of the centerline of the spring model.
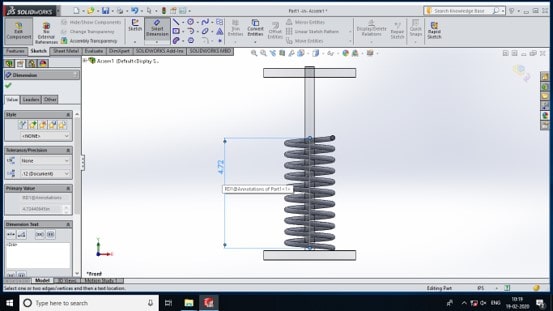
- Increase the length of the centerline of the spring model to around 180mm and approve the dimension change.
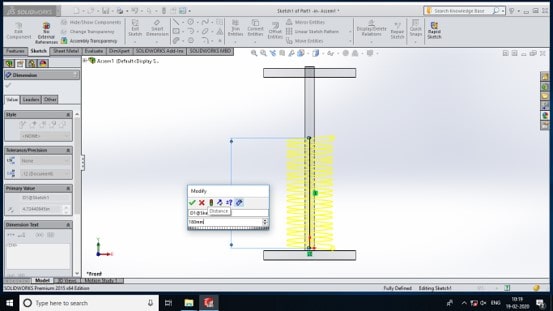
- Now delete the dimension since we don’t need them.
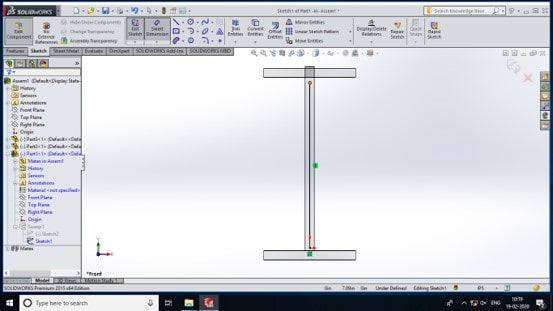
- Now select the smart dimension and select the distance between the top end of the spring to the lower edge of the upper section. Alter it to 5 mm and then approve the change and exit the menu. You’ll have to exit 2 times to enter the assembly screen.
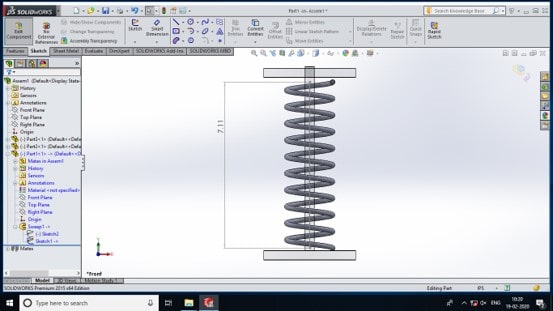
- If you have done everything correctly then you’ll get a model like the one given below. Save the assembly.

- Now enter the Motion Assignment option as shown in the figure below.
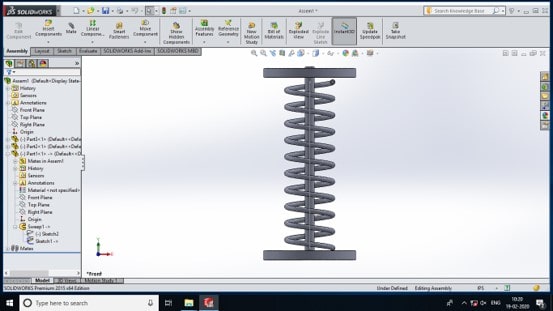
- Now move the animation timer to around 8 seconds.
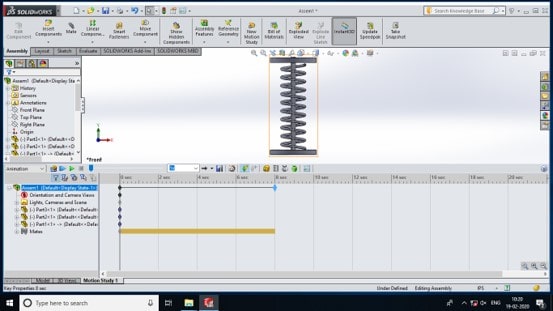
- Then select the motor option. For the sake of simplicity, we will use motor animation.
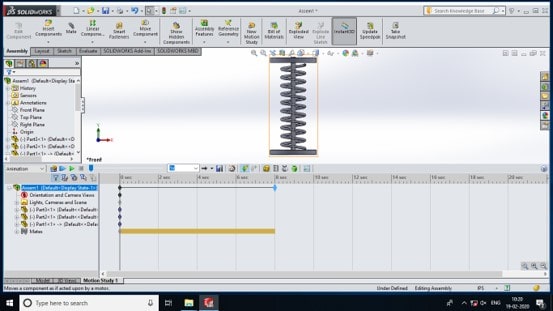
- Change the motor type to the linear motor(Actuator).
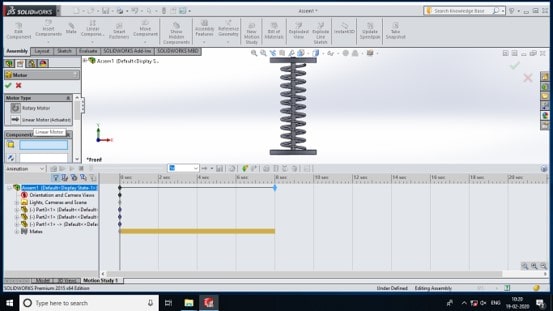
- Now, let's give the necessary information in the Component/Direction option.
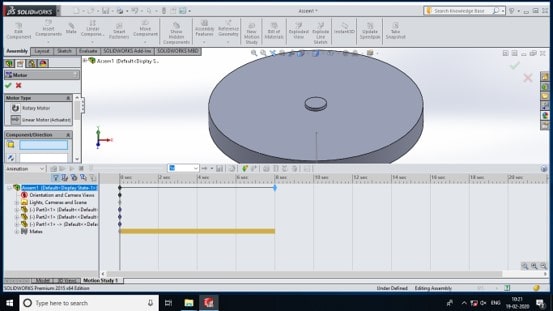
- In component part give the Extruded Cut profile of the upper part.
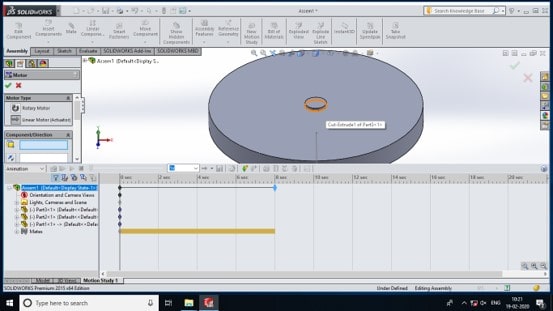
- In the direction give the direction upward of the Extruded Cut Profile.
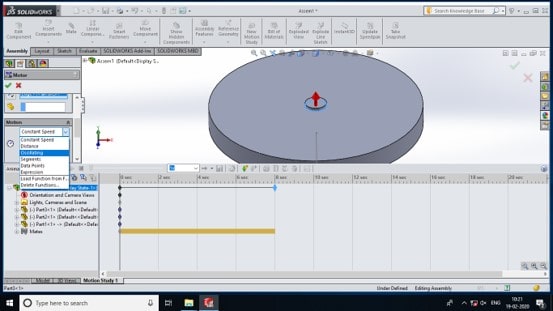
- In Motion Select Oscillating, set the range of movement to approximately 50mm.
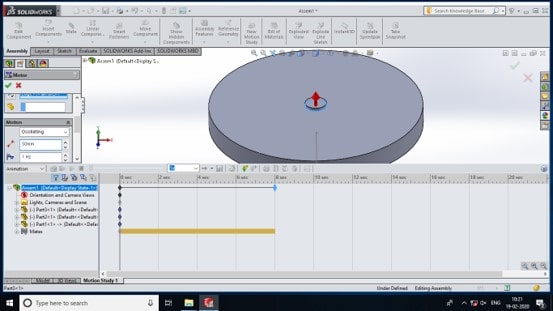
- And select the frequency to 0.5 Hz. And set the degree equal to 90 degrees.
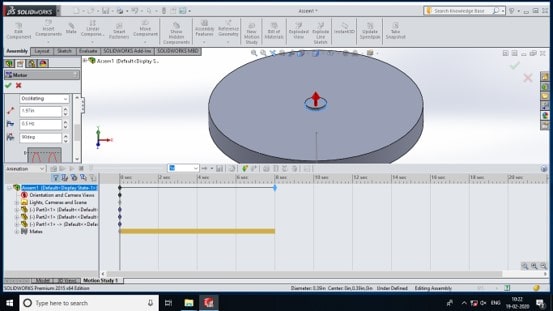
- Now approve the changes and the work is completed.
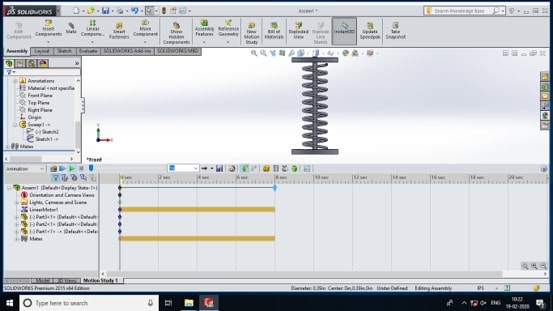
- Press the play button to animate the movement of the spring under load. This is animation is only to make to understand the different features of SolidWorks. Don’t use it for scientific purposes.
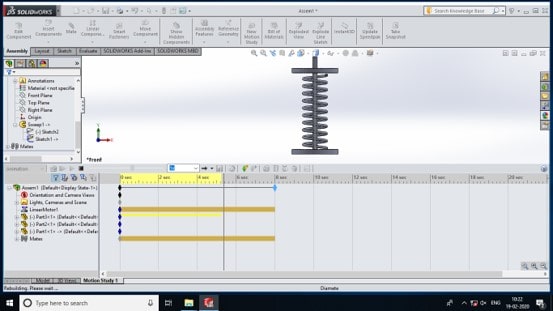
- Screenshot of the animation.
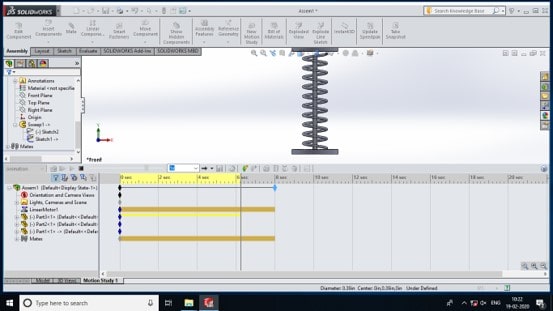
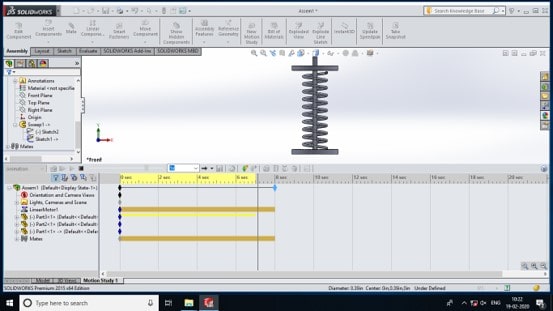
.