Batch Costing Assignment Help
It is a form of specific order costing. In job costing, costing of jobs that are executed against any specific order is done whereas in batch costing, items are manufacturer for stock. A finished product comprises of different materials, so assembling of different components for the final product is required.
In this type of costing, items are produced in bulk no single unit of a product is produced. It is a type of job costing only. In batch costing, separate cost sheet is prepared for specific batch by assigning a batch number.
Cost P.U. = Total Cost of that batch / Number of Units Produced by that batch
Material cost, labor cost and other overheads are recovered batch wise. Such a method is used in pharmaceutical or drug industries, ready-made garments, radio-sets etc.
Batch Costing Features:
- Batch is treated as a cost unit.
- Cost are accumulated and ascertained for each batch.
- Single cost sheet is not prepared for all the batches. Specific cost sheet is prepared for specific batch and batches are assigned numbers through which they can be identified.
- Cost P.U. will be ascertained by dividing total cost of batch by number of units produced by batch.
Batch Costing Assignment Help By Online Tutoring and Guided Sessions from AssignmentHelp.Net
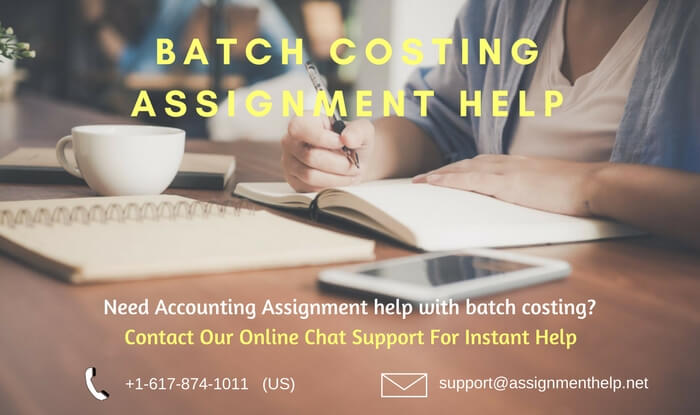
Batch Costing Applications
Generally, applies in the firms which are into manufacturing similar articles in definite batches either for internal consumption or sale to consumers.
Industries like:
- Ready-Made Garment Manufacturing.
- Drug Industries.
- Spare parts and components.
- Toys Manufacturing Industries.
- Tyre and Tubes manufacturing industries.
Economic Batch Quantity
Economic Batch Quantity refers to optimum level of production of quantity of batch at one point so that set up and processing costs and carrying costs are together optimized.
Why there is a need to determine economic batch size?
Generally, it happens that production time is lost while setting up for the production. So, to maximize the level of efficiency and derive maximum benefit and minimize the cost per unit, economic batch quantity is determined.
Two types of Costs are involved in this:
a) Setting up & Processing Costs- It is the cost which is incurred on setting up and processing operations before the start of production of a batch. Relationship between Setting up & processing cost and Batch size is negative.
Larger the Batch Size, Lower will be the set-up costs.
Smaller the Batch Size, Higher will be the set-up costs.
b) Carrying Costs- It is a cost incurred on maintaining the inventory. There is a positive relationship between Batch Size and Carrying Costs.
Larger the Batch Size, Higher the Carrying cost because of high average inventory.
Smaller the Batch Size, Lower the Carrying cost because of low average inventory.
{` EBQ= √2AS/C EBQ = Economic Batch Quantity A = Annual Demand S = Set up cost per batch C = Carrying Cost per unit per year. `}
Illustration-
From the following information, calculate Economic Batch Quantity for a company using batch costing:
{` Annual Demand for the components 3,000 units Setting up cost per batch 500 Manufacturing cost per unit 100 Carrying cost per unit 9% p.a. Solution: EBQ = √2x3000x100/9% of 100 = 258 units `}
Difference between Job Costing and Batch Costing
Job Costing | Batch Costing |
---|---|
Cost is collected according to jobs. | Similar batch units are used as cost units. |
Each job is treated as separate entity. | Separate cost sheet is maintained for each batch. |
Costs are found at the completion of the job. | Cost per unit is determined by dividing the total cost of the batch with number of units produced. |
Job costing is used in printing, furniture etc. | Batch costing is used in drug industries, TV sets, Radio. |
Time taken for execution of job is short. | Process time taken for each article in a batch is less than generally taken for execution of job. |
Need Accounting Assignment Help with batch costing; Submit Your Assignmentwork or contact our online chat support for instant help.