Manufacturer Of Printing Inks Sample Assignment
Sunchem, a manufacturer of printing inks, has five manufacturing plants worldwide. Their locations and capacities are shown in Table 1 along with the cost of producing 1 ton of ink at each facility. The production costs are in the local currency of the country where the plant is located. The major markets for the inks are North America, South America, Europe, Japan, and the rest of Asia. Demand at each market is shown in Table 1. Transportation costs from each plant to each market in US dollars are shown in Table 1. Management must come up with a production plan for 2010.
Table 1 | |||||||
North America |
South America |
Europe |
Japan |
Asia |
Capacity Tons/year |
Production cost/ton | |
United States |
600 |
1200 |
1300 |
2000 |
1700 |
185 |
$10,000 |
Germany |
1300 |
1400 |
600 |
1400 |
1300 |
475 |
15000 Marks |
Japan |
2000 |
2100 |
1400 |
300 |
900 |
50 |
1800000Yen |
Brazil |
1200 |
800 |
1400 |
2100 |
2100 |
200 |
13000 Real |
India |
2200 |
2300 |
1300 |
1000 |
800 |
80 |
400000 Rupees |
Demand (tons/year) |
270 |
190 |
200 |
120 |
100 |
a. If exchange rates are expected as in Table 2, and no plant can run below 50 percent of capacity, how much should each plant produce and which markets should each plant supply?
US$ |
Mark |
Yen |
Real |
Rupee | |
US$ |
1 |
1.993 |
107.7 |
1.78 |
43.55 |
Mark |
0.502 |
1 |
54.07 |
0.89 |
21.83 |
Yen |
0.0093 |
0.0185 |
1 |
0.016 |
0.405 |
Real |
0.562 |
1.124 |
60.65 |
1 |
24.52 |
Rupee |
0.023 |
0.046 |
2.47 |
0.041 |
1 |
b. If there are no limits on the amount produced in a plant, how much should each plant produce?
c. Can adding 10 tons of capacity in any plant reduce costs?
d. How should Sunchem account for the fact that exchange rate fluctuate over time?
Solution
(a)
Sunchem can use the projections to build an optimization model as shown below. In this case, the shipments from each plant to every market are assumed to be variable and solved to find the minimum total cost. This is done by utilizing the following constraints:
- Each plant runs at least at half capacity.
- Sum of all shipments from the plant needs to be less than or equal to the capacity in that plant.
- All production volumes are non-negative.
- All calculations are performed at the exchange rates provided.
Optimization model:
n = 5: five manufacturing plants m = 5: number of regional markets. Dj = Annual tons of ink needed for regional market j Ki = Maximum possible capacity of manufacturing plants. Especially for (a) lower limit for capacity is 50%*Ki . cij = Cost of shipping one ton of printing ink from plant i to regional market j pi = Cost of producing one ton of printing ink at plant i xij = Tons of printing ink shipped from site i to regional market j. It should be integral and non-negative |
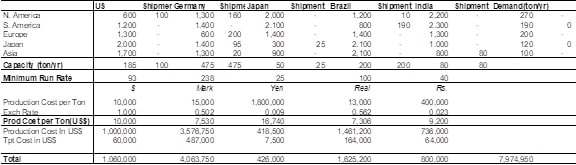
This is clearly influenced by the production cost per ton and the local market demand. Low cost structure plants need to operate at capacity.
(b)
If there are no limits on production we can perform the same exercise as in (a) but without the capacity constraints (5.2) and (5.3). This gives us the following results:
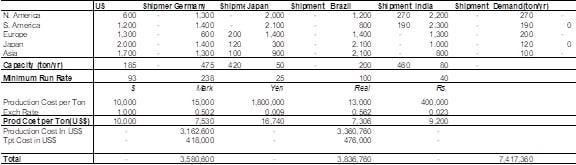
Clearly by having no restrictions on capacity SunChem can reduce costs by $557,590. The analysis shows that there are gains from shifting a significant portion of production to Brazil and having no production in Japan, US and India.
(c)
From the scenario in (a) we see that two of the plants are producing at full capacity. And in (b), we see that it is more economical to produce higher volumes in Brazil. Once we add 10 tons/year to Brazil, the cost reduces to $7,795,510.
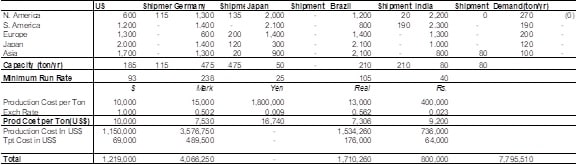
(d)
It is clear that fluctuations in exchange rates will change the cost structure of each plant. If the cost at a plant becomes too high, there is merit in shifting some of the production to another plant. Similarly if a plant’s cost structure becomes more favorable, there is merit in shifting some of the production from other plants to this plant. Either of these scenarios requires that the plants have built in excess capacity. Sunchem should plan on making excess capacity available at its plants.